.png?width=1533&height=712&name=Druckverfahren%20(2).png)
Finishing process
To give you an overview of our wide range of finishing options, we have summarised the most important information.
Screen printing.
Screen printing is a process in which the printing ink is applied to the material through a fine-meshed fabric using a rubber squeegee. A stencil makes the mesh impermeable to the ink in the areas that are not to be printed. This process is particularly suitable for smooth and straight surfaces such as throwing discs, cylindrical to slightly conical shapes (bottles).
Benefits:
- Opaque colours
High resilience of the print motif
Special colours such as Pantone or HKS possible
What data is required?
- Vector data or pixel data with at least 600dpi in 1:1 print size (1C only)
Minimum line thickness of at least 0.3mm in the desired size
Font in paths
Important notes:
- Texts smaller than 1 millimetre are not legible
- Raster prints are only possible very roughly - 24 screen
- Light colours on dark backgrounds may have to be underlaid in white
- The legibility of QR codes must be checked, a sample is recommended in advance
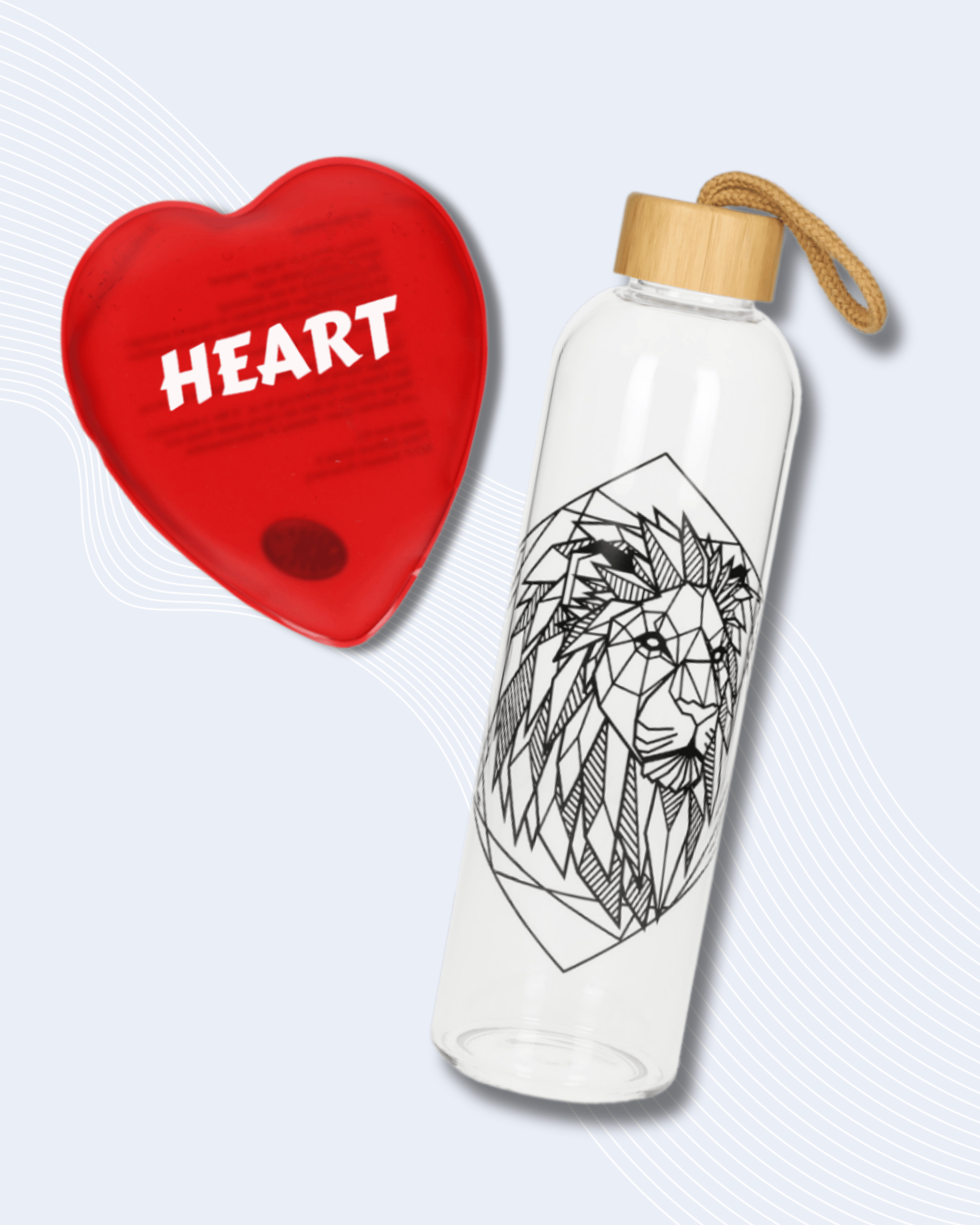
Pad printing.
Pad printing is an indirect gravure printing process in which the printing ink is transferred from the printing form (cliché) to the item using an elastic silicone pad. This process is particularly suitable for uneven surfaces such as ballpoint pens or yo-yos and is one of the most important processes for printing on plastic bodies.
Benefits:
- Photorealistic printing (4C) and gradients in special colours or 4C possible on request
- Uneven surfaces can be printed with indentations or curvatures
- Very fine details can be printed
What data is required?
- Vector data or pixel data with at least 600dpi in 1:1 print size (1C only)
- Minimum line thickness of at least 0.2mm in the desired size
- Font in paths
Important notes:
- Texts smaller than 1 millimetre are not legible
- Under certain circumstances, light colours on dark backgrounds must be highlighted in white
- The legibility of QR codes must be checked, a sample is recommended in advance
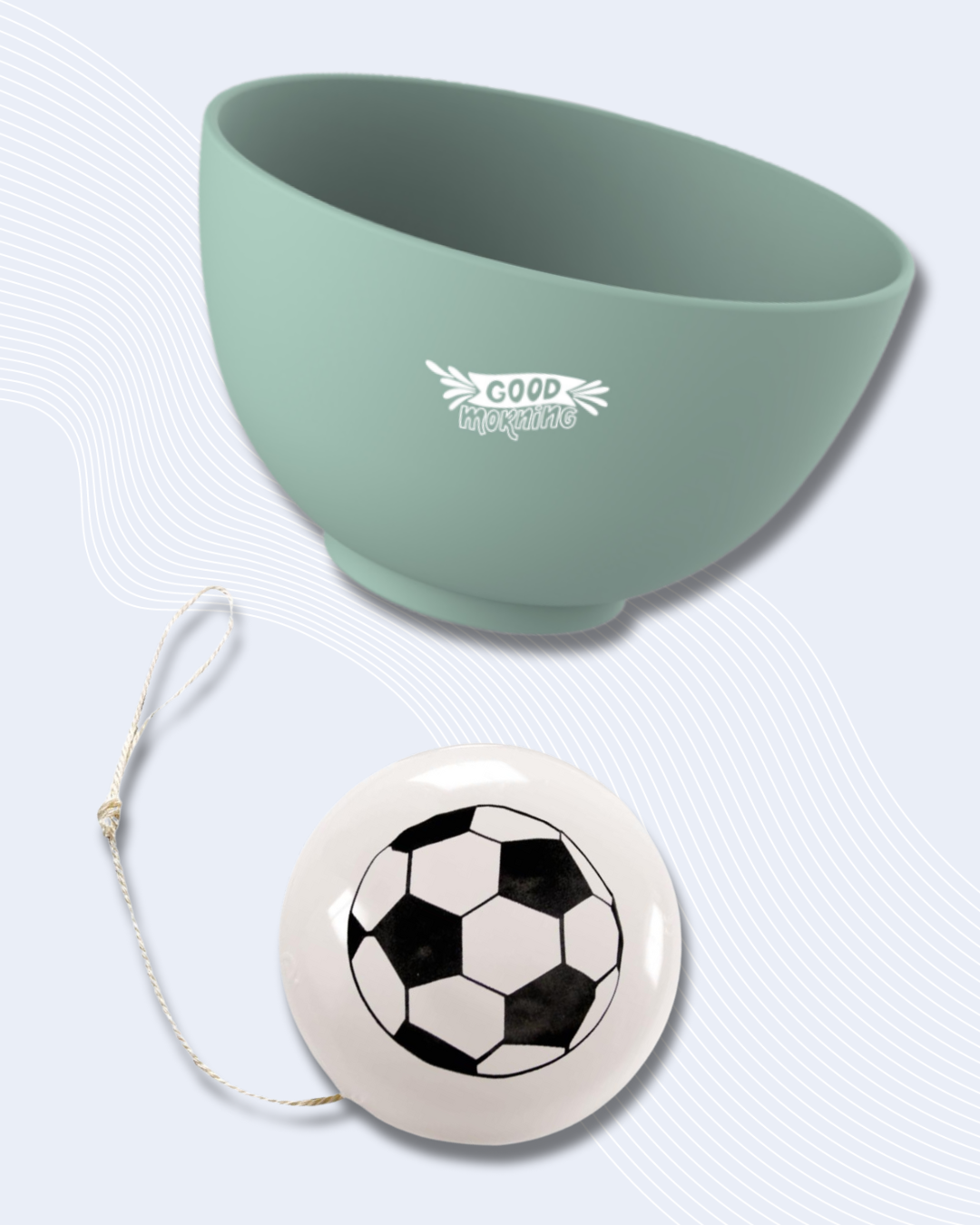
IMould.
In the iMould process, films printed in advance using digital or offset printing are inserted into the thermoforming or injection moulding tool and then back-injected. This finishing technique enables the high-quality and expressive realisation of photorealistic motifs while at the same time reducing production costs. This process is mainly used to finish plastic items with a smooth surface, such as storage containers, trays, snow flies or throwing discs.
Benefits:
- Robust finishing in optimum photo quality
- Screenless reproduction of halftone originals
- Favourable prices
- No lithos, printing plates and pre-press costs
- Possible for plastic surfaces with a smooth surface
What data is required?
- Vector data or pixel data with at least 300dpi in 1:1 print size
- The data must be adapted to our templates
- A 3mm bleed must be taken into account
Important notes:
- The IMould film consists of a white base material (transparent film on request)
- Print in CMYK
- Special colours can only be adapted approximately and with deviations
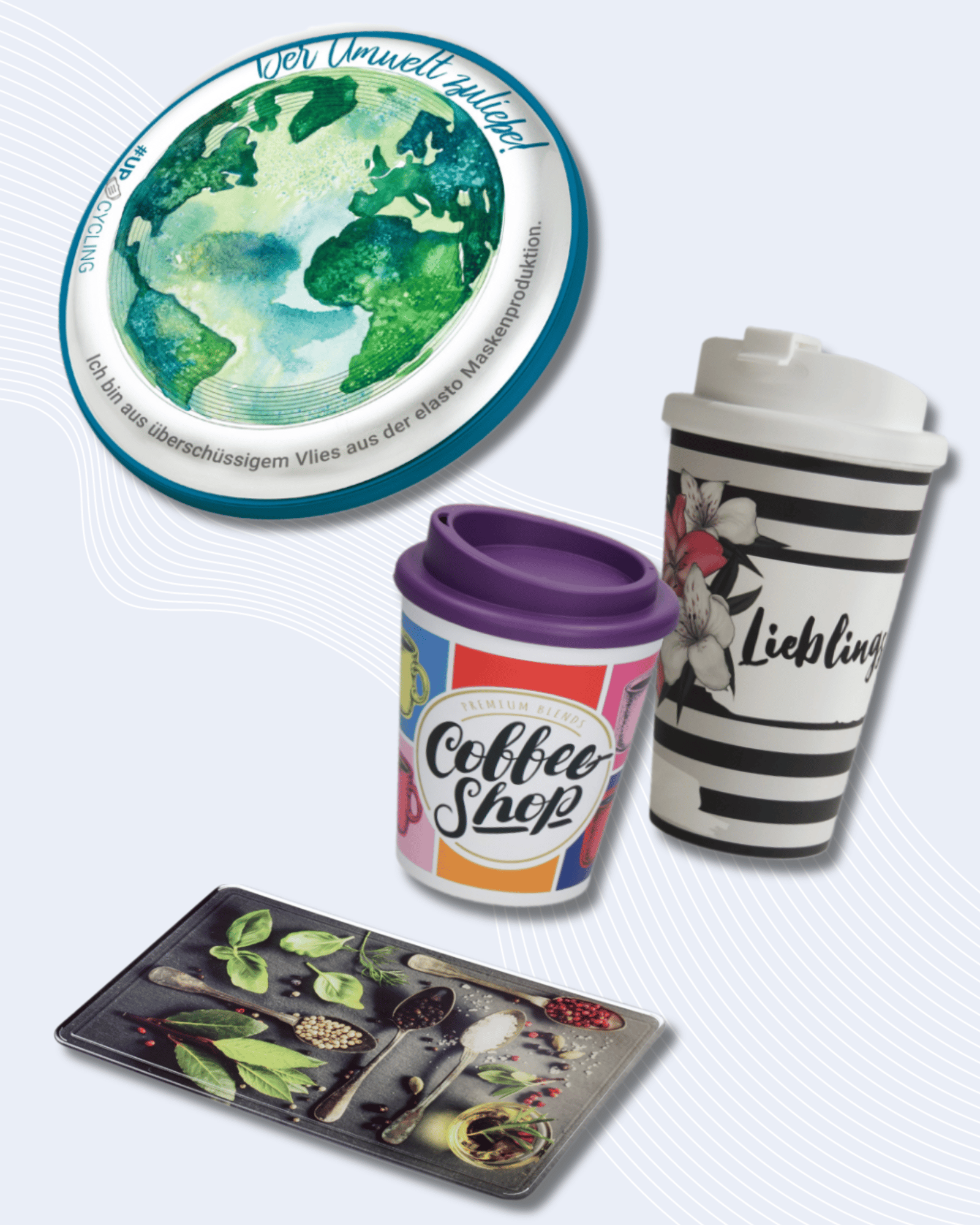
UV digital printing.
UV digital printing is a large-format printing process that can be used to print on almost any material. The applied colour is cured by UV light during the printing process. This means that plastic items with a smooth surface, such as sliding puzzles, parking discs, ice scrapers, magnets or rulers, can be printed in a very short time and packaged or assembled immediately.
Benefits:
- Robust finishing in optimum photo quality
- Screenless reproduction of halftone originals
- Favourable prices - even for small print runs
- No lithos, printing plates and pre-press costs
- Possible for plastic surfaces with a smooth surface
What data is required?
- Vector data or pixel data with at least 300dpi in 1:1 print size
- Print in CMYK + white underlay (partial white printing possible)
- Special colours can only be adapted approximately and with deviations
Important notes:
- Special colours can only be adapted approximately and with deviations
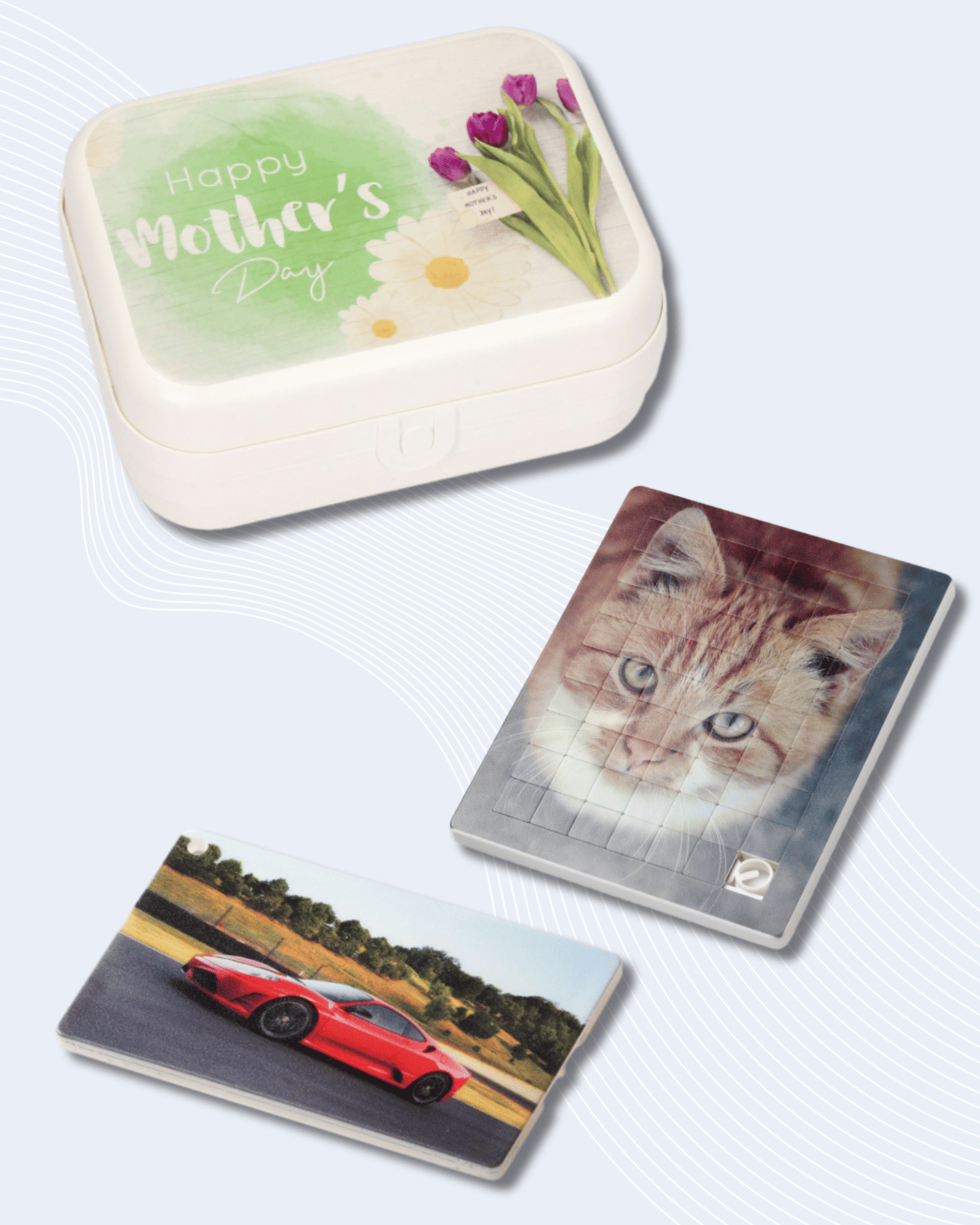
PremioTouch.
The PremioTouch printing process refines items such as drinking bottles in three steps: White underlay, motif printing and lacquering. This technique creates a haptic, brilliant finish and is therefore unique.
Benefits:
- Robust finishing in optimum photo quality
- Screenless reproduction of halftone originals
- No lithos, printing plates and pre-press costs
- All-round printing possible
- Special, raised feel
What data is required?
- Vector data or pixel data with at least 300dpi in 1:1 print size
- Minimum line thickness of at least 0.3mm in the desired size
- Font in paths
- Print in CMYK + white + varnish
Important notes:
- Texts smaller than 1 mm are not legible
- Dust inclusions and small irregularities may occur with full-surface motifs
- Special colours can only be adapted approximately and with deviations
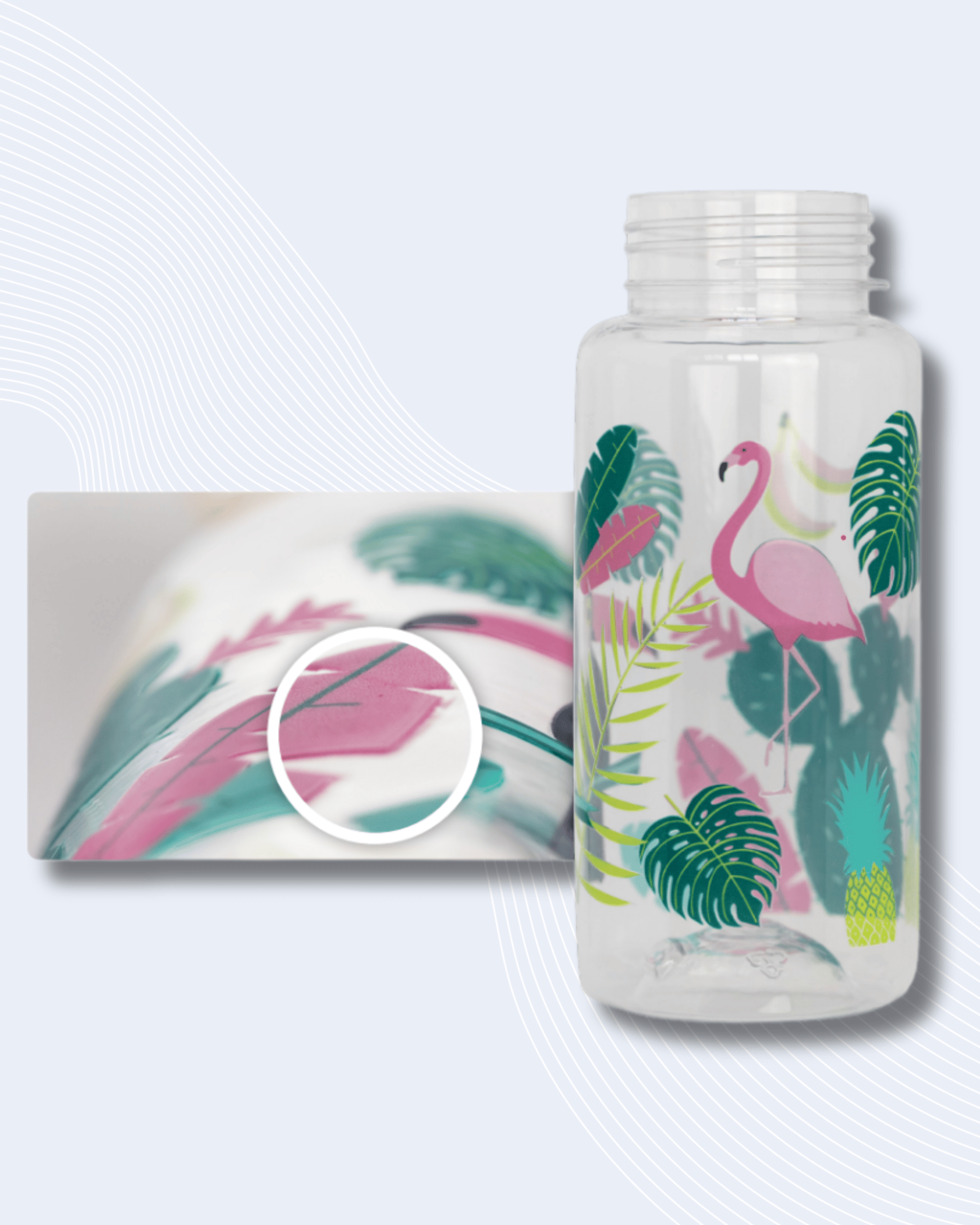
Fibre laser/Co2 laser/UV laser.
Laser engraving is the labelling or marking of items with a laser beam. Depending on the laser source, metal, wood, glass or even special plastics can be enhanced. The engraving is durable, does not fade and is waterproof and smudge-proof.
Benefits:
- Long-term advertising effect
- Variable characters and graphics of any type and size are possible
- Small print runs from 1 piece
- Personalisation
What data is required?
- Only vector data possible.
Important notes:
- Deviations in surface finish, colour and laser are unavoidable
- Exactly opposite finishing cannot be guaranteed, the position of the motifs may vary
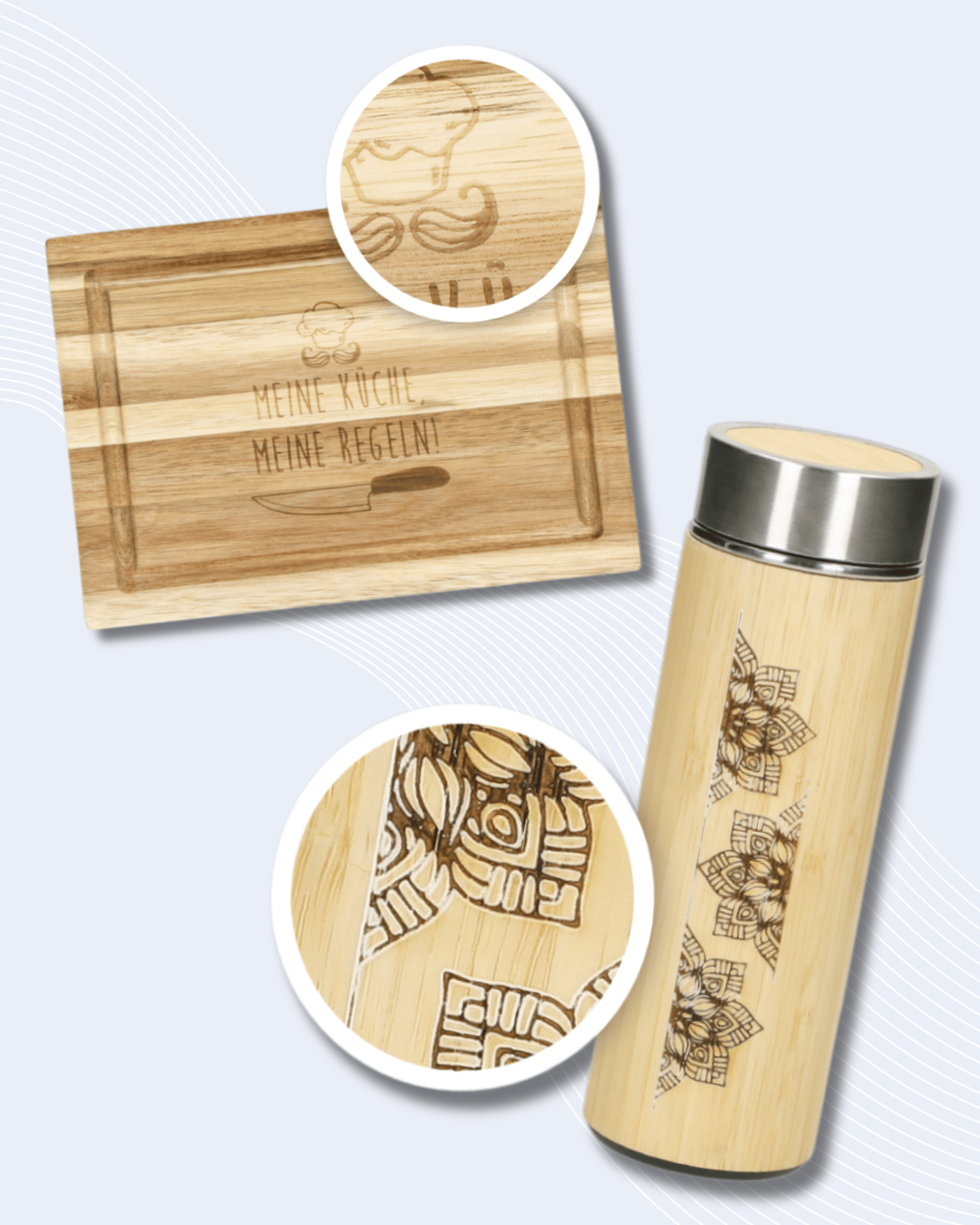
Technical terms.
RGB stands for the three primary colours red, green and blue. These three colours are the physical primary colours, which is why the display in the digital sector is based on RGB. RGB is referred to as an additive colour model, as colour perception is created by mixing light. The more colour is used, the brighter the image becomes. If all three primary colours are used at 100%, the result is white.
-Jun-27-2024-08-41-27-3747-AM.png?width=1500&height=1500&name=Design%20ohne%20Titel%20(1)-Jun-27-2024-08-41-27-3747-AM.png)
CMYK is made up of three colours - cyan, magenta and yellow - and the key colour (black), which are usually printed on a white background. CMYK is also known as process colours. The more colour is applied, the darker the result. This is therefore referred to as a subtractive colour model. Key colour is necessary because applying 100 % cyan, magenta and yellow does not produce a true black, but a dark brown. The individual colours are printed on the paper one after the other, creating all possible colour nuances depending on the mixing ratio.

Solid colours
Solid or spot colours are ready-mixed colours. Spot colours have several advantages over process colours. They can be used to print colour tones that cannot be achieved by mixing process colours (CMYK). These are, for example, metallic and neon colours, but also gold, silver and opaque white. Depending on the colour tone, spot colours can also have a stronger luminosity than process colours.
Colour fans are used to define spot colours. The best-known manufacturers of spot colours and publishers of colour guides are Pantone, HKS and RAL.
White underlay
On dark substrates, a white underlay with opaque white is necessary for screen, transfer and pad printing, as light solid colours in particular are not opaque enough due to their nature.
Minimum line thickness
The minimum line width is the minimum width of a line or dot. Depending on the type of finishing, different guideline values apply for the minimum line width. The finer the elements in the logo or print motif, the more likely it is that elements or lines will appear interrupted, uneven, blurred or torn. In principle, the following guidelines apply depending on the motif and type of finishing:
Positive elements and lines: always at least 0.3 mm minimum line thickness
Negative elements and lines: always at least 0.5m minimum line width
-Jun-27-2024-08-42-06-3390-AM.png?width=1500&height=1500&name=Design%20ohne%20Titel%20(2)-Jun-27-2024-08-42-06-3390-AM.png)
Trimming
Bleed is a format allowance that is necessary for the printing process. The bleed allowance protrudes from the final format and is intended to prevent white bleed. The bleed is then removed when cutting to the final format.